Inicio / Moldeo por inyección de PEEK
Moldeo por inyección de PEEK
El plástico PEEK, un plástico de ingeniería especial de muy alto rendimiento, tiene unas propiedades físicas y químicas perfectas. El PEEK se ha convertido en un material fundamental en campos como la aviación y la industria de semiconductores. Gracias a la tecnología de moldeo por inyección de precisión, el PEEK puede satisfacer exigencias estrictas que van desde instrumentos quirúrgicos mínimamente invasivos (<0,1 mm de grosor de pared) hasta juntas de exploración de pozos profundos (150 MPa de presión).

Por qué elegir el moldeo por inyección de PEEK
Las piezas moldeadas por inyección de PEEK demuestran un rendimiento notable en entornos extremos en comparación con plásticos comunes como el PP, el ABS y el nailon. Mientras que los plásticos ordinarios no pueden soportar altas temperaturas y son propensos a la deformación y la corrosión, el PEEK mantiene un funcionamiento estable a 260°C. Además, los productos moldeados por inyección de PEEK presentan una gran solidez y resistencia a los ácidos fuertes. Por ello, el plástico PEEK es ideal para fabricar componentes de precisión resistentes al desgaste, como piezas de motores aeroespaciales e implantes médicos.
- Resistencia a altas temperaturas: Servicio continuo a 260°C, tolerancia a corto plazo hasta 300°C.
- Resistencia mecánica: Resistencia a la tracción 90-100 MPa, 4 veces la resistencia al desgaste del PTFE
- Estabilidad química: Resistente a ácidos fuertes (excepto ácido sulfúrico concentrado) y disolventes orgánicos
- Estabilidad dimensional: Índice de contracción 0,1-0,5%, coeficiente de dilatación térmica similar al del aluminio metálico
- Ignifugación: Clasificación UL94 V-0, retardante de llama sin halógenos
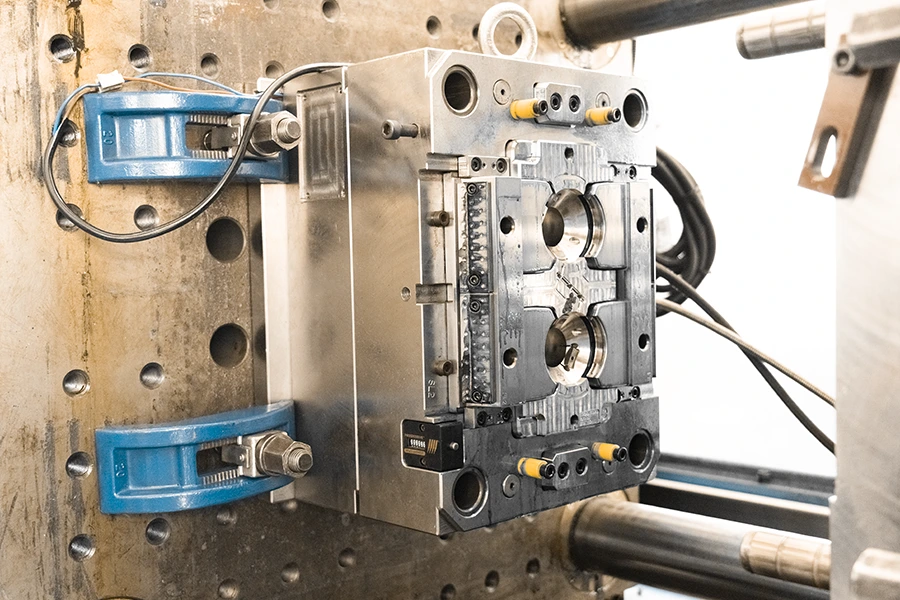
¿Qué productos se pueden fabricar con el moldeo por inyección de PEEK?
Aunque las piezas moldeadas por inyección de PEEK son costosas, resultan insustituibles en estas aplicaciones de alto rendimiento:
Ámbito médico
Aplicación
- Jaulas de fusión espinal
- Cabezales de sellado para endoscopios
- Carcasas de marcapasos
¿Por qué?
- Biocompatibilidad: Sin rechazo para implantes de larga duración (certificado por la FDA).
- Transparencia radiográfica: No interfiere con las imágenes postoperatorias.
Aeroespacial
Aplicación
- Asientos de válvulas de combustible satélite
- Conectores de mazo de cables de avión
- Soportes de motor para drones
¿Por qué?
- Reducción de peso de 30%: Equivale a una mejora de la eficiencia de combustible de 5%
- Resistencia criogénica: Mantiene la resistencia a -60°C
Equipamiento industrial
Aplicación
- Juntas de bombas químicas
- Rodamientos para la industria alimentaria
El moldeo por inyección de PEEK también puede producir núcleos de válvulas de precisión para cafeteras, bisagras plegables para smartphones capaces de más de 100.000 ciclos de apertura/cierre y carcasas para drones submarinos que soportan entornos subacuáticos de alta presión. Con el continuo desarrollo de productos en IA y robótica, el papel del moldeo por inyección de PEEK será aún más prominente.
PP
PE
PC
PVC
ABS
PA
POM
PBT
PMMA
PEEK
¿Cuándo se puede evitar el uso de material PEEK?
Si el diseño de su producto se enfrenta a un presupuesto limitado, escasez de material o exceso de prestaciones, estas alternativas pueden resultar más rentables.
Escenario 1: Presupuesto limitado - ¿Puede utilizarse un material más barato?
Criterios: Cuando su pieza funciona por debajo de 150°C y no entra en contacto con ácidos / álcalis fuertes.
Solución recomendada:
Alternativa: PEI (coste reducido por 30%-40%)
Un caso real: Después de cambiar a PEI para una caja de cambios industrial:
- Costes reducidos en 35%
- Funcionamiento estable durante 5 años en entornos lubricados a 120°C.
Escenario 2: Escasez de material PEEK - ¿Qué hacer?
Soluciones de emergencia (orden de prioridad):
- PEKK: El rendimiento más parecido al PEEK, pero requiere aumentar la temperatura de moldeo entre 10 y 15 °C.
- PPS: Alternativa a corto plazo para piezas estructurales no portantes.
- Nylon de alta temperatura: Sólo para uso temporal (vida útil reducida por 50%).
Comparación del moldeo por inyección de PEEK y PEI
El núcleo de la comparación entre PEEK y PEI en el campo del moldeo por inyección reside en su rendimiento y coste. Ambos plásticos presentan resistencia a altas temperaturas, resistencia a la corrosión y propiedades similares. Aunque sus prestaciones son comparables, existe una diferencia de coste significativa (normalmente, el PEEK es 2-3 veces más caro que el PEI). Aunque otros plásticos (p. ej., PPS, LCP) pueden igualar parcialmente sus prestaciones, no pueden sustituir al PEEK y al PEI en parámetros críticos (p. ej., biocompatibilidad, resistencia a la fatiga a largo plazo). Por tanto, los ingenieros deben equilibrar rendimiento y coste para seleccionar el material óptimo.
Dimensión | PEEK | PEI | Puntos de decisión sobre el diseño |
Rendimiento térmico | Temperatura de uso continuo: 250°C | Temperatura de uso continuo: 170°C | El PEEK es obligatorio para entornos de alta temperatura (>200°C). |
Punto de fusión: 343°C | Tg: 217°C | ||
Rendimiento mecánico | Resistencia a la tracción: 100 MPa | Resistencia a la tracción: 85 MPa | Elija PEEK para aplicaciones de alta carga; PEI para resistencia al impacto. |
Módulo de flexión: 3,6 GPa | Módulo de flexión: 3,0 GPa | ||
Parámetros de procesamiento | Temperatura del barril: 360-400°C | Temperatura del barril: 340-370°C | El PEI tiene un tiempo de ciclo más corto y es adecuado para piezas complejas de paredes finas. |
Temperatura del molde: 160-180°C | Temperatura del molde: 140-160°C | ||
Compatibilidad química | Resistente a ácidos fuertes (excepto H₂SO₄ concentrado) y disolventes orgánicos. | Resistente a combustibles y ácidos débiles; poca resistencia a los álcalis | Utilice PEI para la exposición a combustibles; PEEK para entornos químicos agresivos. |
Costes y procesos | Coste del material: Alto | Coste del material: Medio | Dar prioridad al PEI en caso de restricciones presupuestarias, pero evitar la exposición prolongada al calor. |
Requiere moldes de alta temperatura para evitar las babosas frías | Propenso a parpadear; requiere un control preciso de la presión | ||
Aplicaciones clave | Retenes de aceite, herramientas quirúrgicas, componentes de satélites | Carcasas de sensores de automoción, aisladores de PCB, equipos esterilizados por vapor | Utilice PEEK para implantes médicos; PEI para encapsulación de componentes electrónicos. |
¿Cómo elegir un proveedor fiable de servicios de moldeo por inyección de PEEK?
Encontrar un proveedor de moldeo por inyección de PEEK supone muchos retos para las empresas de nueva creación o de diseño:
- Producción de piezas de alta precisión en plazos ajustados
- Gestión de costes por ensayo y error con presupuestos limitados.
La elección de un procesador de PEEK no cualificado puede acarrear graves consecuencias. Por ejemplo, se rumorea que una empresa médica se asoció con una fábrica de moldeo que se desviaba solo 2℃ en el control de la temperatura, lo que provocó que componentes de implantes por valor de $1,2 millones cristalizaran y se fragilizaran en masa, retrasando el proyecto más de seis meses.
1. Experiencia en moldeo de precisión a alta temperatura
El moldeo de PEEK requiere mantener una temperatura de fusión de 380-400℃ de forma constante. Los equipos reacondicionados en fábricas genéricas sufren a menudo fluctuaciones de temperatura superiores a ±5℃. First Mold emplea máquinas de inyección totalmente eléctricas con control de temperatura de bucle cerrado y consigue una estabilidad de ±1,5℃. En 2024, 13 de los 17 proyectos de PEEK incluyeron paredes ultrafinas, logrando una tasa de éxito en el primer disparo de 92%+ gracias a esta precisión.
2. Trazabilidad de materiales sin concesiones
Aproximadamente 35% de las llamadas piezas "PEEK" del mercado están adulteradas con PEI o PPSU, más baratos. Los proveedores reputados proporcionan la certificación UL para cada lote de material. FirstMold no sólo divulga los informes de ensayo de las materias primas, sino que también permite a los clientes participar en la verificación por espectroscopia FTIR de terceros, eliminando los riesgos de falsificación en origen.
3. Respuesta ágil controlada por el riesgo
Cuando una empresa de robótica necesitó urgentemente rediseñar moldes de juntas PEEK en 48 horas debido a cambios de diseño, First Mold aprovechó los sistemas modulares de canal caliente prediseñados para reducir drásticamente el tiempo de modificación de moldes de la media del sector de 72 horas a sólo 19 horas. Esta agilidad está impulsada por una base de datos estandarizada de más de 50 diseños de moldes dedicados a PEEK.