Home / Manufacturing Services / Injection Molding Service / Overmolding Service
Overmolding Process | Precision Multi-Material Manufacturing
A two-step injection molding technique to combine rigid plastics with soft, durable overlays. First Mold’s precision mold manufacturing and high-quality overmolding production are highly recognized worldwide.
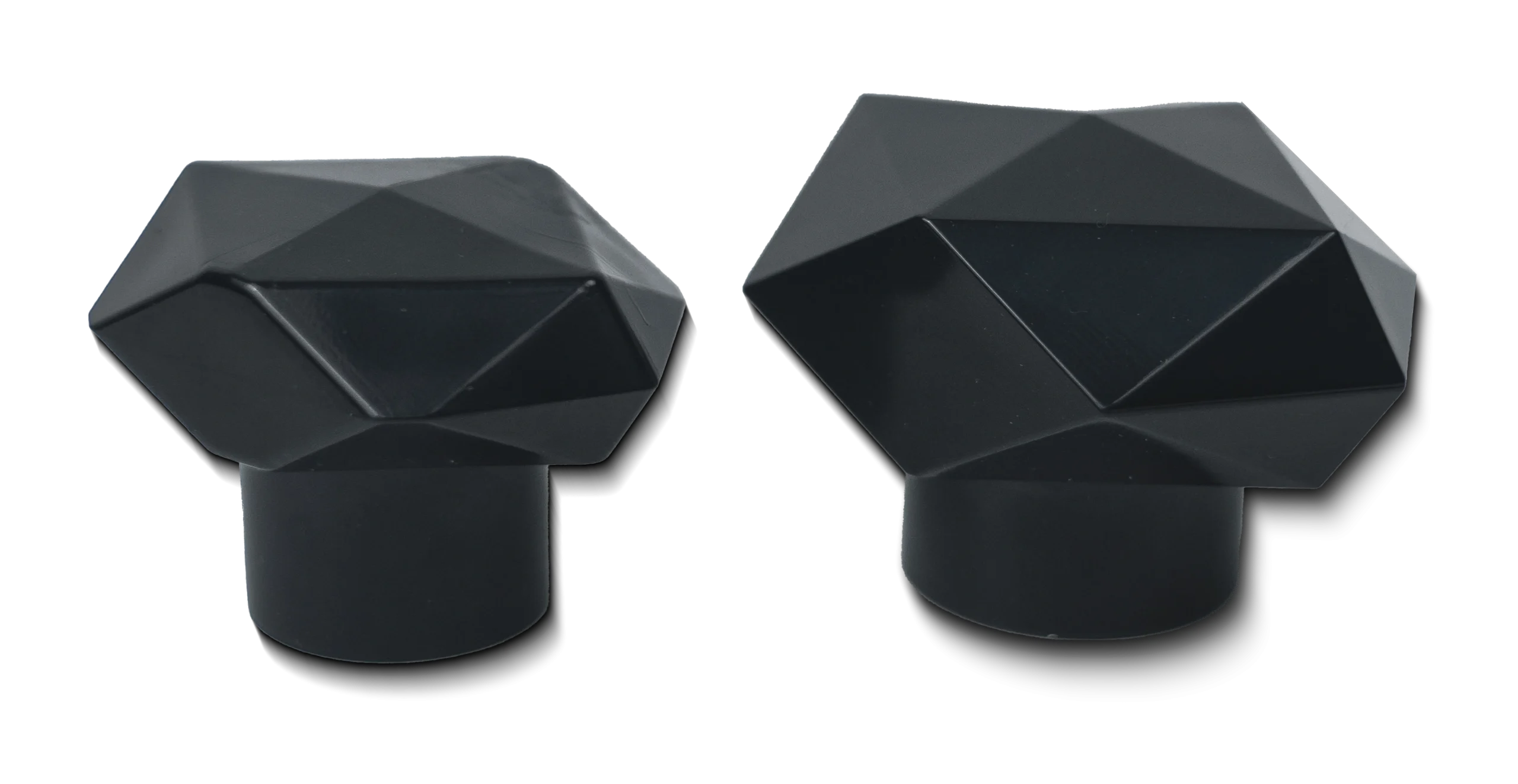
What is Overmolding?
In product design, some of your products may have a soft material (such as TPE, silicone, or rubber) wrapped around a base material (hard plastic or metal). This is done to improve grip, prevent slipping, or enhance appearance. Such products are quite common, like tool handles, toothbrush grips, and phone cases. Their production usually requires a overmolding process.
Overmolding involves using two different plastic materials, injected separately in one injection molding machine. After the first molded in one set of molds, the product is taken out and placed into another set of molds for the second injection molding. Therefore, overmolding typically requires two sets of molds.
No More Slippery Handles — Bond, Seal, Protect with Overmolding
First Mold leads the injection molding industry with comprehensive capabilities. Overmolding stands as one of our proven specialties. We solve tough overmolding problems like:
Fixing Production Defects
- Delamination: Soft material peels off easily due to insufficient adhesion with hard substrate.
- Flash: Excess material creates rough edges, driving up finishing costs.
- Sink Marks: Uneven cooling causes surface dents, ruining looks and durability.
- Material Lab: Test 300+ material pairs, deliver compatibility reports.
- Precision Molds: ±0.5°C temperature control eliminates flash.
- Real-time pressure monitoring: Auto-adjust pressure to prevent sink marks.
Addressing Design Pitfalls
- Conflicting wall thickness: Over-thick hard layers cause soft material cracks; under-thick layers lack strength.
- Visible parting lines: Molten plastic overflow at shut-off surface ruins premium product aesthetics.
- Fast DFM reviews: Get wall thickness tips within 48 hours.
- Patented mold positioning: <0.02mm error between base and overmold.
- Hidden parting lines: Seamless solutions for electronics/medical devices.
Overmolding Applications and Case Studies
Injection Molding Factories use overmolding in a wide range of industries.
Industry | Representative Products | Key Advantages |
Medical Devices | Surgical instrument grips, Prosthetic components, Catheter connectors, Syringe plungers | Biocompatibility (ISO 10993), Chemical resistance, Enhanced sterilization compliance (FDA/CE) |
Automotive | Steering wheel grips, Airbag modules, Lightweight seat shells, Battery pack housings | 40-50% weight reduction, Vibration damping (SAE J1475), Flame retardancy (UL94 V-0) |
Consumer Electronics | Phone cases, Earbud charging cases, Game controller grips, Smartwatch bands | Anti-slip & shock absorption, IP68 waterproofing, Seamless multi-color aesthetics |
Industrial & Tools | Power tool handles, Wrench anti-slip sleeves, Precision instrument housings | 300% impact resistance improvement, MIL-STD-810G compliance, Ergonomic fatigue reduction |
Case Studies:
Challenge
Frequent drops cause TWS earbud cases to crack. This leads to a 23% user complaint rate.
Solution
Hard PC inner shell and TPU shock-absorbing overmold
Surface Treatment
Skin-like matte texture, fingerprint-resistant finish
Results
A Top 3 global smartphone brand reduced after-sales repair costs by 41%
Material combinations for overmolding technology
Overmolding technology is a paradigm of multi-material integrated manufacturing in industrial production, with diverse material pairing options. First Mold summarizes the material combination strategies for Overmolding as follows:
Functional Synergy
i.e.: Combining polypropylene (PP) with SEBS elastomers leverages molecular chain entanglement to eliminate adhesives, while achieving gamma sterilization resistance (25kGy dose) for medical-grade handles
Performance Enhancement
i.e.: Nylon (PA66)-TPV elastomer composites exhibit exceptional resistance to oil/acid corrosion and ultra-low friction (μ=1.2). It’s ideal for high-voltage battery housings in electric vehicles.
Sustainable Innovation
i.e.: Bio-based TPE fused with PLA substrates delivers fully biodegradable solutions. By cutting carbon emissions by 50% means it meets EN 13432 industrial compostability requirements—revolutionizing eco-packaging systems.
Substrate | Overmold | Typical Applications | Certification Standards |
PP | TPE/SEBS | Medical handles, tool grips | ISO 10993, FDA 21 CFR |
ABS | TPU | Phone cases, smartwatch bands | IEC 60529, RoHS |
PC | Liquid Silicone Rubber (LSR) | Automotive transparent buttons, baby pacifiers | IATF 16949, LFGB |
Nylon (PA6/PA66) | TPV | Automotive battery housings, industrial gears | UL94 V-0, MIL-STD-810G |
PBT | Glass-fiber reinforced TPE | Power tool handles, connectors | EN 61340, IEC 60695 |
PEEK | Fluorocarbon Rubber (FKM) | Aerospace sensors, medical implants | ISO 13485, AS9100 |
Metal Inserts | TPE/TPU | Power tool handles, medical devices | ISO 2768, ASTM D638 |
POM | Thermoplastic Elastomer (TPE) | Gear damping sleeves, precision instrument housings | DIN 54800 |
PPS | Silicone Rubber (VMQ) | High-temperature sensors, engine components | SAE J2460, AMS 3217 |
PLA | Bio-based TPE | Eco-friendly packaging, biodegradable products | EN 13432, ASTM D6400 |
Overmolding Vs. Insert Molding Vs. Two-color molding
Overmolding involves injecting one material onto an existing substrate (such as hard plastic or metal). This process is completed in separate steps to form a protective or functional layer. In insert molding, the inserts such as metal or electronic components are placed into the injection mold first. Then, plastic is injected to secure and integrate the inserts. In two-shot molding, a rotating mold is used to inject two different materials in the same cycle.
Dimension | Overmolding | Insert Molding | Two-Color Molding |
Process Steps | Two-step injection: Hard core → Soft overmold | Pre-insert placement → Single-shot encapsulation | Dual-shot injection (rotating/sliding mold) |
Material Combination | Soft-hard bonding (e.g., PP+TPE) | Plastic + metal/insert (e.g., PA66+copper) | Dual-color plastics (e.g., ABS+PC) |
Equipment Requirements | Standard machine + compatible mold | Standard machine + robot/manual insert placement | Dedicated two-color machine + rotating mold (±0.02mm) |
Material Interaction | Chemical bonding (thermodynamic compatibility) | Mechanical locking (no chemical bonding) | Physical layering (melting point synchronization) |
Structural Difference | Layered encapsulation (functional integration) | Insert core (composite reinforcement) | Seamless layering (aesthetic fusion) |
Mold Cost | $$ | $ | $$$ |
Production Cycle | 30-60 sec (requires cooling between layers) | 45-90 sec (manual insert placement) | 20-40 sec (automated dual-shot) |
Typical Products | Tool handles, medical instruments | Automotive connectors, medical electrodes | Dual-color taillights, translucent keyboard keys |
FAQ
How to determine if my product is suitable for Overmolding? What key parameters need to be provided in advance?
We recommend providing the following three categories of parameters for evaluation:
1. Material Compatibility:
Polarity parameters of the rigid substrate (e.g., ABS/PC) and soft material (e.g., TPE/TPU).
Melting point difference (ΔT ≤50°C preferred).
If data is unavailable, we can perform material library matching tests.
2. Structural Feasibility:
Thickness of rigid parts must be ≥1.2mm to withstand secondary molding pressure.
0.3-0.5mm gaps should be reserved in soft material coverage areas to prevent injection molding flash.
3. Functional Requirements:
Mark stress points for anti-slip, sealing, or shock-absorption applications.
Example: Grip areas of medical handles require enhanced bonding strength.
How does First Mold rapidly address delamination during small-batch overmolding production?
Our 48-Hour Closed-Loop Commitment:
Root Cause Analysis:
- If no melting traces at interface → Design flaw (Add snap-fit features or undercuts)
- If incomplete melting layer → Process flaw (Adjust soft material injection temperature to hard material's Tg +15℃)
Solutions:
Three optimization packages: Material substitution/Surface treatment/Structural upgrade
(Example: TPE-V self-bonding material eliminates pretreatment)
Cost Assurance:
- 100% material cost coverage for rework caused by our process errors.
How does First Mold handle precision control for tiny overmolding products like earphone parts?
With rich experience in micro-precision manufacturing, we maintain micron-level accuracy through three key methods:
1. Mold Making
- Super-smooth spark erosion (Ra≤0.02μm)
- High-precision 5-axis cutting
- Sealing surface gap ≤0.005mm
2. Process Control
- Stable injection pressure (≤1% variation)
- Precise temperature control (±0.5℃)
3. Inspection
3D laser scanners (±5μm precision)
X-ray CT scanning
Detects bubbles as small as 0.1mm³
How flexible is your production capacity for sudden order increases (overmolding only)?
We ensure agile capacity expansion through 3 core strategies for overmolding order surges:
1. Equipment Redundancy & Quick-Start Mechanism
- Dedicated Equipment Pool:
12 overmolding-specific injection molding machines (180-2500T clamping force), with 4 strategically reserved machines (33% of total) on standby. - Rapid Changeover Capability:
≤45-minute mold switching (industry average: 2 hours) via preheated hot runners and standardized mold base interfaces.
2. Deep Supply Chain Integration
- Strategic Raw Material Inventory:
3-month safety stock (≈500MT) for high-frequency material combinations (TPE-PP, TPU-ABS). - Supplier Priority Response:
VMI agreements with Covestro and ExxonMobil ensure 72-hour delivery of critical materials (TPE, LSR).
3. Dynamic Capacity Allocation & Smart Scheduling
- AI Capacity Prediction System:
Adjusts production plans using historical data and real-time load analysis. For example: - Pre-allocates backup capacity 2 weeks prior to predicted 50% medical handle order increases
- Automatically prioritizes urgent orders within ≤4 hours
- Shift Flexibility:
Seamless transition from 2-shift to 3-shift operations increases daily output by 50% (100k→150k units).
How to verify the feasibility of Overmolding process with minimal cost during small batch trial production?
We offer a three-stage verification solution:
- 3D printed prototypes: Using hard resin + soft silicone rubber molding, single-unit cost <50 RMB, verifying assembly and tactile experience.
- Soft mold trial production: High-temperature resistant PEI molds with aluminum frames, costs only 20% of steel molds for up to 500 units.
- Mold frame reuse: If insert molds already exist, soft rubber cavities can be added to save 30% of mold development costs.
How to ensure accurate color matching for multi-material overmolding products? what color difference standards are used?
We use a two-step color control system: Preparation:
Match color materials with Pantone guides using precision instruments to create color formulas (max 1.5 color difference).
Real-time check: Use camera systems during production to monitor and adjust colors instantly.
Quality standards: Follow ISO rules - color difference within batches ≤0.8, between batches ≤1.2.