Home / ABS Injection Molding
ABS Injection Molding
The ABS (Acrylonitrile Butadiene Styrene) plastics continue to be a key material in the injection molding industry, with the global injection molding grade ABS market expected to reach $2.6 billion by 2030, growing at a CAGR of 5.1% from 2024 to 2030. The ABS injection molding process is increasingly being used to produce high-quality, durable parts and components in industries like automotive, electronics, and consumer goods.
What Is ABS Injection Molding?
ABS injection molding is an industrial manufacturing process to process abs resin into the desired plastic shape.
First, the manufacturer designs and processes the injection mold according to the product requirements and installs it on the injection molding machine. Next, the abs plastic pellets are melted into a fluid in the injection molding machine, injected into the mold at high pressure, and then cooled and cured, resulting in a molded part that is the target plastic product. Mold fabrication and abs material molding are the key stages in the whole process.
The precise design and processing of the mold affects the shape and precision of the product.
The injection, pressure holding, cooling and other steps in material molding determine the quality and performance of the product.
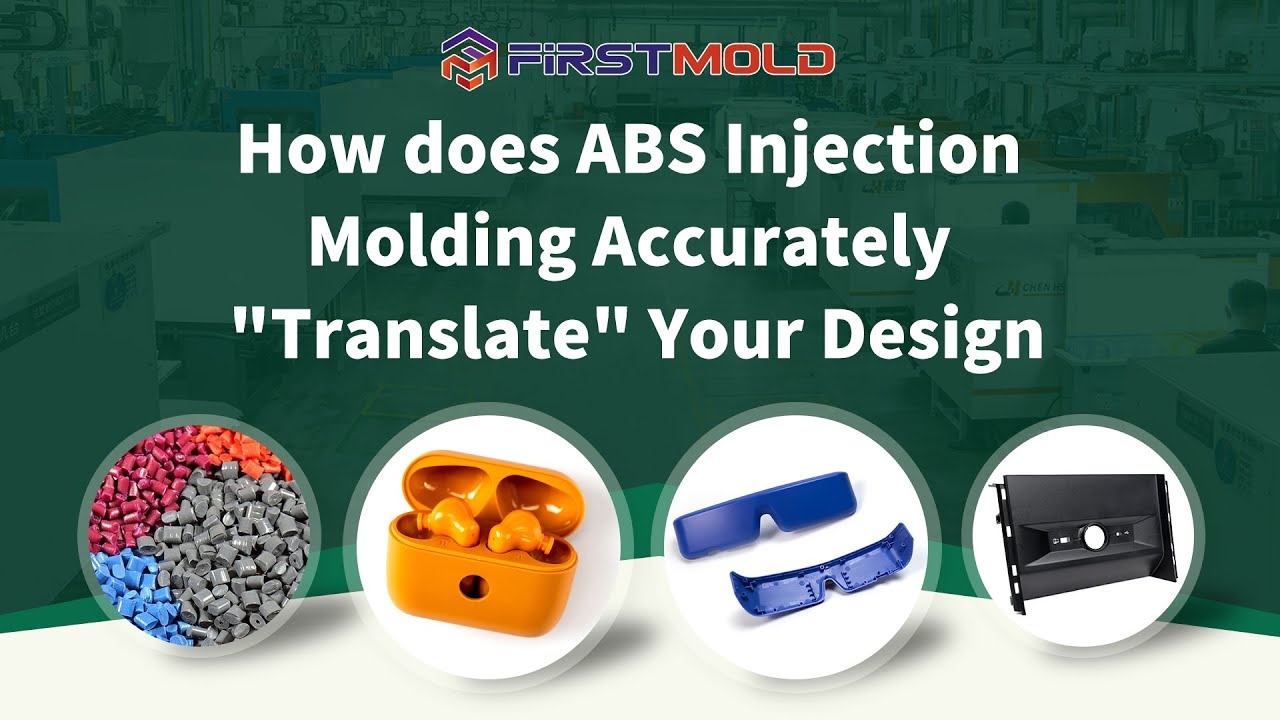
Tips: If you’re new to ABS material, simply click ‘ABS Plastic‘ to learn more.
Wide Range of ABS Injection Molding Applications Across Industries
ABS plastic fabrication’s applications span various industries due to its durability, strength, and aesthetic appeal.
The ABS injection molding process can achieve high-precision ABS molding, fabricate complex shapes, ensure efficient production, and also enable various surface treatments to meet the performance and appearance requirements of automotive parts.
The ABS molding process can meet diverse appearance demands and has high production efficiency, which can keep pace with the large-scale production rhythm of consumer electronics products.
With appropriate safety and chemical resistance, ABS materials can precisely manufacture components that meet the strict size and shape requirements of medical devices. Moreover, they can maintain stable performance during the cleaning and disinfection processes and can also produce efficiently to meet the supply demands of medical device parts.
ABS plastic molding can satisfy the strength, toughness, and stability requirements for the daily use of household items. Its ABS injection molding process can produce various shapes and sizes of household components. The efficient production can adapt to the batch production mode of household products, and at the same time, it can achieve diverse surface effects to match the household style.
Automotive & EV
- Dashboard trim panels
- Automotive HVAC systems
- Under-the-hood components
- Interior trim
- Airbag system enclosures
- Automotive lighting systems
Consumer Electronics
- Wireless speaker housings
- Components for smart thermostats
- Laptop housings
- Game controller enclosures
- Connectors for consumer electronics
Medical Devices
- Portable medical devices
- Housings for diagnostic equipment
- Laboratory instruments
- Pharmaceutical devices
- Medical sensor enclosures
Home Appliances
- Enclosures for kitchen gadgets
- Blender bases
- Microwave door panels
- Vacuum cleaner casings
- Robotic cleaners
ABS plastic fabrication is widely used in both everyday life and industrial applications, and the examples listed above are just the tip of the iceberg. First Mold has extensive experience with injection molding using ABS resins, including the use of modified ABS materials (PC+ABS, ABS+PA, ABS/PBT, Flame-Retardant ABS, etc.).
Key Advantages of Choosing ABS Molding
Through the various features of ABS injection molded parts, we can easily understand the multiple advantages of ABS injection molding.
High Molding Precision:
Good dimensional stability: After ABS plastic injection molding, ABS materials exhibit relatively small dimensional changes, maintaining the designed dimensions effectively. This is crucial for manufacturing components with high dimensional accuracy requirements, such as small plastic brackets in car engine compartments. Their precise dimensions ensure good cooperation with other components.
High replication precision: The ABS injection molding process accurately replicates the shape and details of molds. The products produced have high consistency and repeatability, even for components with complex shapes and fine structures. For example, ABS injection molding for electronics ensures that the size, shape, and tactile feel of tiny buttons in consumer electronics are highly consistent.
Manufacturing Complex Shapes:
High design freedom: The ABS injection molding process allows for the molding of various complex shapes, with minimal restrictions on form. Designers can fully utilize their creativity and design products with unique appearances and structures. For example, custom ABS molding can easily create household items like creative vases and uniquely shaped lamps with streamlined designs.
Integration of multi-functional parts: The process can integrate different functional parts into a single ABS molding part, reducing the number of parts and assembly processes. This improves production efficiency and product reliability. For example, in an ABS injection molding for automotive parts, various control buttons and display mounting positions can be integrated into a single molded part.
According to statistics, ABS material has the highest usage rate in all injection molding projects at First Mold.
Find the Right ABS Injection Molding Manufacturer
An outstanding ABS injection molding service provider should possess injection molding machines of various specifications and models, which can adapt to the production of ABS plastic products with different sizes, shapes and complexity levels. The manufacturer should also have a large number of injection molds and extensive experience in ABS product manufacturing, as well as complete mold facilities and a comprehensive quality inspection system.
First Mold is precisely such an excellent company that can offer one-stop ABS injection molding services.
The inspection of qualified suppliers should cover the following aspects:
Advanced Equipment And Personnel
The injection molding machines should be equipped with high-precision injection systems, and the clamping systems should have sufficient pressure and precision, as well as good temperature control systems. There should be a professional mold design team and sophisticated mold manufacturing equipment.
Extensive Production And Manufacturing Experience
The team has a comprehensive understanding of the characteristics of ABS plastics, masters multiple injection molding processes and has the ability to optimize the processes. It can provide various surface treatment services and is capable of quality control.
Scientific Quality Control Measures
Best plants can conduct raw material inspections, process quality control and finished product quality inspections. They have obtained relevant quality certifications, can comply with the standards of relevant industries and meet the customized quality requirements of specific clients.
ABS Injection Molding Cases
Custom ABS molding demands meticulous drying and process control to mitigate moisture-related defects, warping, and shrinkage, alongside precise mold design to ensure quality finishes and part integrity. Accordingly, engineering and technology that possess the necessary engineering and advanced machinery skills are required.
Precision ABS injection molding service with small challenges to produce high-quality luggage scale components.
It is a combination of ABS plastic and aluminum materials that are processed through injection molding and mold-making processes.
A simple case of mass production of portable ECG monitor buttons with a wide range of ABS injection molding applications in the medical industry.
ABS manufacturing service in producing calculator housings with injection molding ro discover how the parts be made.
ABS Overmolding to make a visually stunning and functionally precise perfume cap presented a unique challenge.
ABS Molding FAQ
ABS Molding FAQ
What defects may occur when my ABS plastic products are being produced in an injection molding factory? And how should I conduct the acceptance inspection?
When producing ABS plastic molding products in an injection molding company, multiple defects may arise.
In terms of appearance, there may be flash (burrs), sink marks, weld lines, bubbles, silver streaks, flow marks, etc. There may also be dimensional deviations and deformations.
In terms of performance, issues like insufficient strength and poor toughness may occur.
During the acceptance inspection, for the appearance, visual inspection can be carried out and with the help of dimensional measuring tools to check the surface flatness. Observe from different angles to see if there are various defects and check whether the color is uniform and if there are scratches or stains on the surface.
For dimensional acceptance, calipers and other measuring tools should be used to measure the key dimensions and then compare them with the standard tolerances.
For performance acceptance, physical property tests can be conducted. For example, depending on the application scenarios, tensile, bending or compression tests can be selected to measure the strength, and impact tests can be used to measure the toughness.
If there are specific functions such as electrical insulation and waterproofing, corresponding functional tests also need to be carried out.
What are the common surface treatment methods for ABS injection molded products, and what are their respective advantages and disadvantages?
The common surface finishing methods for ABS plastic injection molded parts include painting, electroplating, and silk screening.
Painting can achieve diverse appearance effects, provide additional protection, and cover up defects, but it involves a complex process, is difficult to control the quality, and has high environmental requirements.
Electroplating can endow products with an excellent metallic texture and improve their wear resistance and corrosion resistance, yet it comes with a high cost, significant environmental impact, and potential adhesion issues.
Silk screening offers high pattern precision, rich colors, and a relatively simple operation, however, its wear resistance is limited, and it is less effective when dealing with large areas. It is ideal for small-batch production or local decoration needs.
How much does ABS injection molding cost?
The price of ABS plastic injection molding is affected by multiple factors.
In terms of raw materials, the prices of ABS plastic materials vary depending on different brands, models, and places of origin. For example, the price of ABS DG - 417 is about $1,510.5 per ton, that of Taiwan's PA - 757 is about $1,888.1 per ton, and that of AG15A1 is about $1,608.4 per ton.
Regarding the complexity of products, the price of simple and small products ranges from $0.1 to a few dollars, while that of complex, large-sized, and high-precision products can reach from dozens of dollars to several tens of dollars.
When it comes to mold costs, the price of simple molds ranges from $500 to several thousand dollars, and that of high-precision ABS molding can reach tens of thousands of dollars.
The production batch size affects the cost allocation. The unit price of products is high in small-batch production, while it decreases in large-batch production.
In terms of processing techniques, the cost of ordinary ABS molding processes is low, and special processes such as two-color ABS injection molding will increase the price due to the complexity of equipment and processes.
Can the ABS injection molding process be replaced by the injection molding of other materials?
Replaceable materials and processes:
Modified PP:
Cost advantage: It has a relatively low price and can reduce production costs. For example, in some injection molded products of daily necessities and toys that are cost-sensitive, using modified PP to replace ABS injection molding can significantly reduce material costs while ensuring certain performance.
Performance characteristics: It has advantages such as good heat resistance, low odor, and a short molding cycle. When its rigidity and toughness are similar to those of ABS molding, the injection pressure required is less than half of that of ABS materials, and the molding cycle is also significantly shortened. In addition, the yellowing resistance of modified PP is far superior to that of ABS materials, making it suitable for products with high requirements for color stability.
ASA:
Its mechanical properties are similar to those of ABS injection molding. It has good chemical resistance and high impact strength, and performs particularly well in terms of weather resistance. It is more suitable for outdoor applications and can replace ABS plastic molding in the injection molding of products such as automobile rearview mirror housings and radiator grilles.
PCT:
It is a high-performance, semi-crystalline thermoplastic polyester. Its mechanical properties are similar to those of polyethylene terephthalate (PET), but it has better hydrolysis resistance and heat resistance and a higher melting point. It is suitable for products with high heat resistance requirements in the electronics and automotive industries, such as plug connectors, relays, switches, and distribution boxes. In these application scenarios, it can replace ABS injection molding for automotive parts.
PSU:
It has excellent mechanical properties, heat resistance, and chemical stability and can replace ABS injection molding in some fields with high-performance requirements, such as some injection molded parts in the aerospace and medical device fields.
Reasons for not being completely replaceable:
Unique performance:
ABS plastic injection molding has comprehensive properties such as good rigidity, hardness, processing fluidity, and high toughness. In some specific fields, such as occasions where high requirements are placed on the surface hardness, impact strength, and dimensional stability of products, the performance of ABS plastic molding is difficult to be completely replicated by other materials. For example, in the manufacturing of the housings of some high-end electronic devices, the comprehensive performance of ABS injection molding materials can better meet the requirements of the products.
Process adaptability:
The ABS injection molding process is relatively mature. For some products with complex shapes, its fluidity and formability during the injection molding process can better ensure the quality and precision of the products. However, when other materials are used to injection mold some products with complex structures, problems such as insufficient filling and warping deformation may occur.
Market and cost factors:
As a widely used engineering plastic, ABS injection molding has a sufficient market supply, relatively stable prices, and cost advantages in large-scale production. For some mature product production lines, if materials are to be changed, it is necessary to re-evaluate the applicability of molds, adjust injection molding process parameters, and may also face risks such as unstable raw material supply and rising costs.
What factors should be mainly considered when designing molds for ABS injection molding to ensure the smooth demolding and good formation of products?
When designing molds for ABS injection molding, multiple factors need to be carefully considered to ensure the smooth demolding and good formation of products.
In terms of demolding, a reasonable draft angle should be designed, generally between 0.5° and 1.5°. And for the undercut structures of products, appropriate demolding mechanisms such as sliders (suitable for vertical undercuts on the side) and lifters (used for internal undercuts) should be adopted. For the cooling system, the location and size of the cooling channels should be carefully arranged. The diameter is usually 6 - 12mm to ensure uniform cooling and avoid local overheating or overcooling that may affect the product accuracy.
When designing the injection molding gate, the position should be selected at the thicker wall part and avoid the appearance or critical parts to reduce weld lines. At the same time, the type of gate should be determined according to the shape and size of the product. For example, a pinpoint gate can be used for small and simple products, and a side gate or a submarine gate can be selected for large and thick-walled products.
The parting surface design follows the principle of simplicity, and is selected at the maximum contour of the product to ensure good sealing. The precision is controlled within a flatness error of 0.05mm to reduce the processing difficulty and the generation of flash.