Home / Manufacturing Services / Mold Making Service / Injection Mold Making Service
Plastic Injection Mold Making
Plastic injection mold making is a precision process for manufacturing custom injection molds. First Mold provides globally high-quality injection mold solutions with our advanced equipment and mold design team.
- Available for rapid toolings and production toolings.
- Utilizes leading brand equipment such as Haas, GF+, and Makino.
- Achieves an accuracy of ±0.0254mm (±0.001″).
- Turnkey injection mold solutions
If needed, we can sign an NDA agreement before providing the quote.
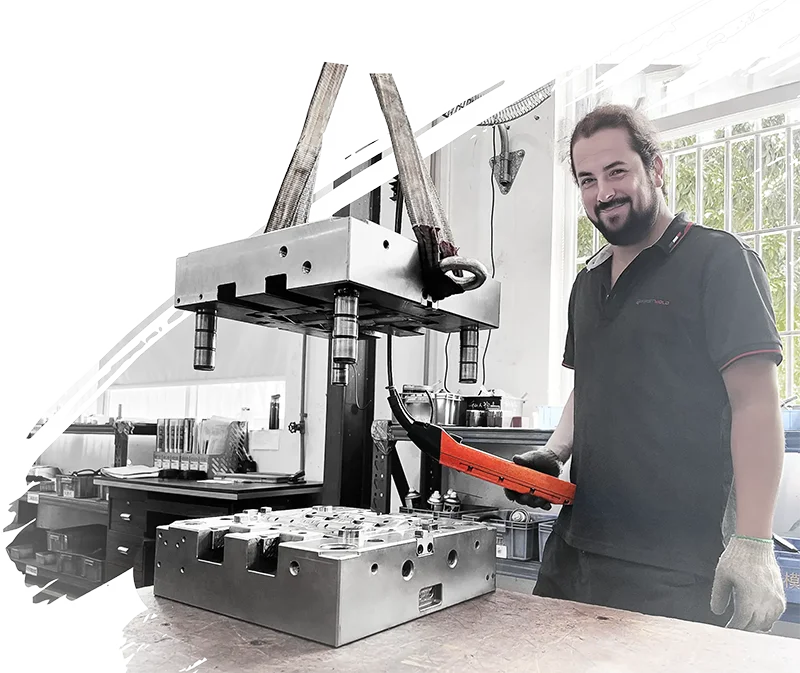
What is Injection Mold Manufacturing?
Injection mold manufacturing is a precision process that converts materials such as tool steel, pre-hardened steel, and aluminum alloys into customized molds through specialized machining and fabrication techniques. At its core, the goal is to leverage the unique properties of these materials to create durable, repeatable tools capable of producing high-precision plastic parts. This allows product designers to not only validate prototypes but also scale to mass production at a million-unit scale.
As the foundational step of the injection molding process, mold fabrication is an indispensable step in plastic part manufacturing, bridging design concepts to tangible, high-volume outputs.
Types of Mold Manufacturing Services We Offer
The injection molds we manufacture can be classified into several categories based on different criteria:
By Usage Frequency:
- Rapid Tooling
Designed for quick, short-run productions, allowing for fast prototyping and testing.
- Production Tooling
Built for long-term, high-volume manufacturing, ensuring durability and stability throughout the production process.
By Material:
- Aluminum Molds
Preferred for their quicker machining time and lower cost, suitable for lower volume productions.
- Steel Molds
Chosen for high-volume production due to their superior durability and longevity.
- Beryllium Copper Molds
Utilized in specific parts of the mold that require unique properties, such as thermal conductivity, in beryllium copper alloyed molds.
By Demolding Mechanism:
- Two-Plate Molds
The simplest and most common type, where the mold splits into two halves to eject the part.
- Three-Plate Molds
More complex, allowing for automatic demolding and the creation of more intricate parts, with an additional plate for runner and gate system separation.
Many clients worldwide have had various types of molds manufactured at First Mold
“As a product engineer, I needed a partner who could handle both low-volume prototype molds and high-volume production tooling. First Mold’s team delivered a multi-cavity P20 steel mold that cut our development time by 30%. Their expertise in thin-wall molding for our IoT devices was a game-changer – no more sink marks or warping issues. Now, we’re scaling to 500k units with zero defects.”
Alex Johnson
Senior Product Engineer
“Managing automotive projects requires molds that survive 500k+ cycles. First Mold’s hardened S136 steel molds for our EV battery housings exceeded expectations. They even suggested a conformal cooling design that reduced cycle time by 15%. Plus, their ISO-compliant documentation sped up our supplier audits.”
Sarah Thompson
Project Manager
Workflow of Mold Making Service
At First Mold, our systematic mold manufacturing workflow ensures precision-engineered solutions, typically structured into six key phases:
1. Product Analysis & Mold Design
Based on the product’s structure, material, and customer requirements, First Mold conduct feasibility analysis and manufacturing feasibility assessment (MFA). Our mold designers then create detailed 3D CAD models and technical 2D engineering blueprints for all mold components.
3. Precision Mold Machining
Components such as cavities and cores undergo rough cutting, high-precision milling, and surface treatment. Processes include CNC milling, electrical discharge machining (EDM), and precision wire-cutting technology.
5. Trial Molding and Optimization
Trial runs are conducted on First Mold’s high-precision injection molding machines. Parameters are recorded, defects are analyzed, and the mold is optimized to ensure seamless production and part consistency.
Injection Mold Solutions Applications
The ultimate goal of the injection mold making service is the production of injection-molded parts. The molds produced can either be used by the clients for their own injection molding production or entrusted to manufacturers for injection molding production.
These two sets of images are molds used in the consumer goods industry and medical molds in their final application during production.
Why We Stand Out
In the manufacturing of injection molds, a quality injection molding factory should prioritize cost reduction for its clients. At First Mold, we fully understand this principle through our collaborations with customers. By implementing innovative strategies to optimize production efficiency and material usage, we consistently help clients lower manufacturing expenses. This commitment to value engineering is precisely why we have secured our position among the top 10 industry leaders.
Global Service Responsiveness
Case: Collaborative multinational delivery for a global consumer electronics brand
Highlights:
China factory + China technical center + Mexico factory collaboration achieved 0% error rate in cross-border project delivery.
7×24 multilingual support reduced average client issue resolution time to <4 hours (industry average: 12 hours).
Technological Innovation & Efficiency Gains
Case: Radio housing injection mold optimization for a global appliance brand
Breakthroughs:
Proprietary runner design technology shortened injection cycle time from 45s to 32s (28.9% improvement).
Reduced product defect rate from 3.2% to 0.8%, saving the client $800,000 annually in rework costs.
Industry-Tailored Solutions
Case: Lightweight new material mold development for a UAV (drone) manufacturer
Innovations:
40% mold weight reduction using advanced materials and composite structures, boosting client production efficiency by 25%.
Improved product yield from 88% to 97%, reducing annual scrap losses by $350,000.
Rapid Delivery
Case: Emergency mass production of battery housing molds for a new energy vehicle manufacturer
Results:
Reduced delivery cycle from 90 days to 55 days through modular design + parallel engineering.
Enabled the client to launch products 1.5 months ahead of schedule, securing 8% market share growth in the first sales quarter.
Injection mold making workshop and department
Advanced Mold Fabrication Techniques and Key Component Production
5-axis CNC centers execute micron-level machining (±0.005mm) for mold bases and core/cavity sets.
Multi-Axis CNC Machining Systems
Precision milling, turning & grinding for complex geometries
High-speed milling of P20/S136 steel |
Hard turning (HRC62+) for pre-hardened components |
Surface grinding with <Ra0.2μm finish |
EDM (Electrical Discharge Machining)
Creating intricate details through controlled spark erosion
Sinker EDM: Forming undercuts and micro-features (0.1mm tolerance) |
Wire EDM: Cutting hardened steels (up to HRC65) with ±0.002mm accuracy |
24/7 automated electrode changing systems |
Integrated Surface Engineering
Combining polishing, texturing & coating
Mirror polishing (SPI-A1 standard) |
Custom textures (VDI 3400/VDA standards) |
DLC/TiN coatings for wear resistance |
Advanced Mold Fabrication Techniques and Key Component Production
Our injection molds are typically fabricated using CNC machining or EDM (Electrical Discharge Machining) processes. The components made for these molds include:
- Mold Base Production
- Core & Cavity Fabrication
- Slider & Lifter Systems
- Custom Inserts & Hot Components
- Injection Mold Guide Pin
- Injection Mold Guide Bushing
- Injection Mold Ejector Pin
- Injection Mold Runner
- Injection Mold Cooling System
Strategic Mexico Facility: Accelerating Mold Making for North America
Except the China base, our Mexico facility in Silao is redefining the standards of plastic injection mold making for the North American market. Positioned strategically to minimize lead times and logistics costs, the facility specializes in rapid tooling, a game-changing solution for businesses seeking speed, precision, and cost-efficiency.
What Can We Do?
DFM
Mold Flow Analysis
Mold Design
Rapid Tooling Production
High-Volume Mold Manufacturing
Insert Molding Tools
Multi-Cavity Mold Solutions
Hot Runner Mold Systems
Aluminum Tooling
Texturing
Surface Finishing
Mold Trial
Mold Maintenance
Mold Repair
Mold Refurbishment
Gate Design
Parting Line Optimization
Mold Assembly
Shorter delivery times
Proximity to key manufacturing hubs across the U.S. and Canada.
Lower costs
Reduced transportation expenses and optimized production efficiency.
Rapid innovation
Accelerate your time-to-market with high-quality molds ready in record time.
Scalable Capacity
Both single prototype or high-volume production molds are acceptable.
- Recommended
FAQ
What Materials Are Commonly Used in Injection Mold Manufacturing?
Injection molds are commonly made from the following materials, chosen based on production requirements, part complexity, and cost considerations:
1. Tool Steel
P20: Pre-hardened steel for medium-volume production (e.g., consumer goods).
H13: Heat-resistant steel for high-temperature plastics (e.g., engineering resins).
S136/S-STAR: Corrosion-resistant steel for optical/medical molds requiring mirror finishes.
2. Aluminum
7075/6061: Used for rapid prototyping or low-volume production due to faster machining and lower cost.
3. Stainless Steel
420/440C: Ideal for high-gloss surfaces or corrosive environments (e.g., PVC molds).
4. Beryllium Copper
Used for inserts in high-heat areas to improve cooling efficiency.
5. Hardened Steel
NAK80/NAK55: For high-precision, long-life molds (e.g., automotive/electronics).
Does your factory offer after-sales services or maintenance for the injection molds you produce?
Yes, reputable mold manufacturers typically provide comprehensive after-sales support and maintenance services to ensure long-term mold performance and customer satisfaction. Here’s what you can expect:
1. Warranty Period
Standard Coverage: Most factories offer a 12–24 month warranty against material or workmanship defects.
Scope: Free repairs or replacements for issues like premature wear, cooling system leaks, or alignment errors.
2. Maintenance Services
Preventive Maintenance:
Regular inspections, cleaning, and lubrication to extend mold lifespan.
Example: Replacing worn ejector pins or polishing cavities to maintain surface finish.
Corrective Repairs:
Fixing damage from misuse (e.g., broken cores, scratched surfaces).
Cost: Often billed hourly or as a flat fee post-warranty.
3. Technical Support
Troubleshooting: Remote guidance for issues like part warping or flash.
Optimization: Adjusting gate sizes or cooling channels to improve cycle times.
4. Spare Parts Supply
Availability: Factories stock critical components (e.g., inserts, sliders, heaters).
Lead Time: Standard parts shipped within 3–5 days; custom parts may take longer.
5. Upgrades & Retrofits
Material Upgrades: Switching to hardened steel for high-abrasion plastics.
Automation Integration: Adding robotics for faster part ejection.
What qualifications and certifications does your injection mold factory have
First Mold, as top 10 injection mold factory, is fully accredited with international quality and environmental standards We hold ISO 9001 certification for quality management and ISO 14001 for environmental management We also comply with industryspecific standards and undergo regular thirdparty audits These certifications and qualifications serve as proof of our commitment to delivering precise reliable and highquality injection mold solutions
How does your factory ensure the quality of injection molds meets customer requirements?
We ensure the high quality of every mold through a comprehensive quality control system and industry-leading technologies. Here’s how we do it:
1. Quality Assurance in the Design Phase
Simulation First:
We use software like Moldflow and AutoForm to perform flow analysis and stress simulation, predicting and optimizing issues like filling, cooling, and deformation in advance.
DFM (Design for Manufacturing) Review:
We collaborate with customers to optimize product design, reducing potential defects (e.g., uneven wall thickness, sink marks).
2. Material and Process Control
Material Certification:
We only use ISO-certified mold steels (e.g., ASSAB, Buderus), with material reports (hardness, composition) provided for each batch.
Precision Machining:
We use high-precision equipment like 5-axis CNC (accuracy ±0.005mm) and mirror EDM (surface roughness Ra<0.1μm).
3. Full-Process Inspection
In-Process Inspection:
Key dimensions are checked using a CMM (Coordinate Measuring Machine) after critical steps (tolerance ±0.01mm).
Surface Quality Inspection:
Surface roughness is measured using white light interferometry to ensure Ra≤0.02μm (medical-grade standard).
4. Mold Testing and Validation
Full Parameter Recording:
During trial runs, we monitor injection pressure, temperature, and cycle time, generating reports for customer approval.
Mass Production Simulation:
Molds undergo 5,000 continuous cycles to verify lifespan and stability (no jamming or deformation).
5. Certification and Standardization
System Certification:
We are certified under ISO 9001:2015 and IATF 16949 (automotive industry) quality management systems.
Traceable Documentation:
Each mold comes with complete documentation (design drawings, inspection data, maintenance records).
6. After-Sales Follow-Up
Free Warranty:
We offer a 12-24 month warranty covering material and workmanship defects.
Quick Response:
Remote or on-site technical support is provided within 48 hours, with spare parts available for emergency repairs within 72 hours.
What is the typical turnaround time for a custom injection mold project?
Our mold delivery timeline begins from the moment you confirm the order and we start the mold design, and it extends up to the first trial run phase.
For rapid tooling, we typically complete the process within 7 days, whereas for production molds, the timeline usually spans 30-45 days. Given that production molds require more time to complete, our team will maintain close communication with you to ensure your requirements are met.
Prior to the first official trial run, we conduct internal trial runs. Additionally, we will undertake 2-3 more trial runs to effectively identify and eliminate potential injection molding defects that could arise during production.
What if modifications are needed after injection mold manufacturing has started
We understand that changes may be required even after production begins our team will promptly assess the requested modifications and discuss the impact on cost and schedule then implement controlled adjustments to ensure the final mold maintains its precision and quality while minimizing disruptions to your project timeline