Plastic products after injection molding often require various patterns or texts to be printed on the surface. This calls for the use of various printing techniques for surface treatment of the parts. Common printing techniques include screen printing, pad printing, lettering, and laser engraving. Today, we’ll delve into the mysteries of screen printing.
Screen printing is a relatively simple technique and therefore is the most commonly used surface treatment technique for plastic parts. Some injection molding factories handle this surface treatment themselves, and FirstMold is one of them.
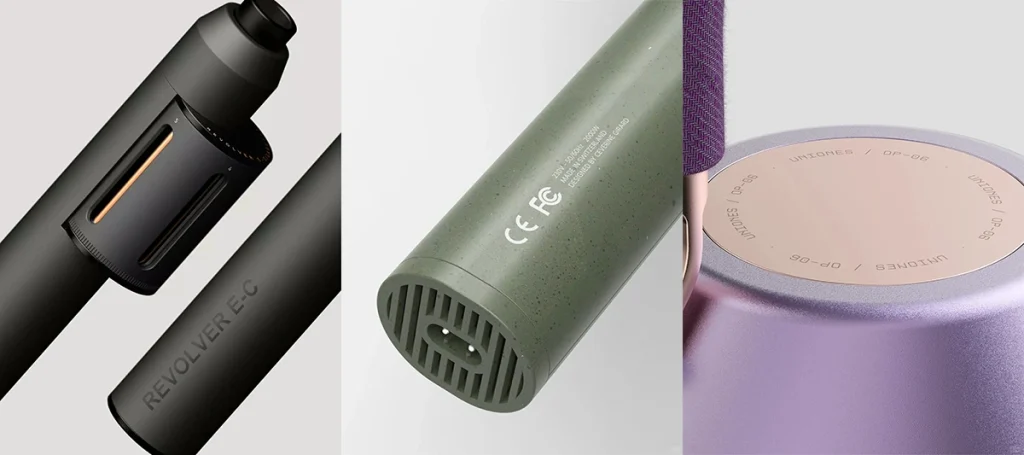
What Is Plastic Screen Printing
Screen printing is the abbreviation of “silk screen printing.” The screen printing technique utilizes a mesh screen to transfer ink onto a substrate(fabric, paper, plastic, or metal), in specific areas to create the desired design or pattern.
Screen printing is an ancient yet widely applied printing method. Depending on the material of the printed object, it can make surface treatment on fabric, plastic, metal, ceramic, glass, lottery, advertising board, stainless steel products, woodblock, lacquerware, etc.
Plastic Screen Printing
Screen printing on plastic parts is one of the secondary machining processes for plastic products. There are various types of plastic products, but in terms of printing methods, flat screen printing is used for sheets and flat surfaces; curved surface screen printing is used for curved surfaces that can be flattened; and indirect screen printing is used for irregular products. Due to the differences in resin, additives, and molding methods of plastic products, there are significant differences in their surface properties, especially in terms of smoothness, polarity, and static electricity.
Characteristics
This technology has many characteristics, with its adaptability being the most fundamental. It can be printed on substrates of different materials and surface shapes without being limited by the size of the printing area. That’s why it’s also called the universal printing method.
The Application Scope of Plastic Screen Printing:
1. ABS plastic: ABS resin plastic, an engineering plastic, has been widely used in various fields of the national economy, including products such as televisions, calculators, etc.
2. Exterior surfaces of plastic components in electronic products: Electronic products, especially digital cameras, MP4 players, televisions, etc., have high demands for appearance. The development of plastic screen printing has facilitated the decoration of electronic products.
3. Plastic labels: In recent years, there has been rapid development in the decoration of plastic labels and graphic texts on plastic parts after molding.
4. Soft and hard plastic parts.
5. Instrument panels.
6. Colored polyester labels.
Comparison with other printing processes
Compared with other processes, screen printing has the following characteristics:
Cost-effective and quick results:
Screen printing can be mechanized or done manually, with investments ranging from a few thousand yuan for individual manual production to tens of millions for building a modern screen printing factory. This method requires lower equipment and material costs compared to other printing methods. Additionally, its plate-making and printing processes are simpler.
Adaptability to irregular substrates:
Screen printing is flexible; it can be applied not only to flat surfaces but also to curved, spherical, or unevenly shaped objects. It can print on various materials such as glassware, plastics, bottles, lacquerware, and wood, which cannot be printed using offset, embossing, or intaglio methods.
Strong adhesion and good ink coverage:
Due to the characteristics of screen printing, ink directly adheres to the substrate through the mesh. Depending on the substrate’s requirements, various inks, coatings, pigments, or pastes can be used for printing. Other printing methods are limited by the fine particle size of pigments in ink.
Thick ink layers and strong three-dimensional effects:
Among the four major printing methods, screen printing produces thicker ink layers, resulting in rich textures and strong three-dimensional effects. The ink layer thickness in screen printing can reach 60 micrometers, compared to 1.6 micrometers for offset, approximately 5 micrometers for embossing, and around 12.8 micrometers for intaglio. Thick-film screen printing can achieve ink layer thicknesses of around 1 millimeter.
Strong resistance to light and good color rendering:
In terms of maximum density values measured after printing black ink on copperplate paper, screen printing can reach a range of up to 2.0, surpassing offset (1.4), embossing (1.6), and intaglio (1.8). In terms of color rendering, even for lightly colored prints, screen printing’s texture and color far exceed those of offset printing.
Wide range of printable materials:
Screen printing can be applied to various materials, including paper, cardboard, wood, metal, textiles, plastics, cork, leather, fur, ceramics, glass, transfer paper, and combinations thereof. Therefore, besides industrial printing, screen printing is widely used in dyeing, apparel, signage, radio, electronics, ceramics, and packaging industries.
Ability to print large formats:
While offset, embossing, intaglio, and flexography are limited by printing format sizes, screen printing can handle large-format printing. Especially with the rapid growth of the advertising market, screen-printed outdoor advertisements have gained increasing prominence. Currently, the largest format for screen-printed outdoor advertisements can reach 2.2 x 3.8 meters and 2.2 x 4 meters.
Design Requirements for Injection Molded Parts:
Design Complexity: Take a good look at how intricate and detailed your design is for the injection molded parts you’re planning to screen print. If it’s complex, you might need fancier printing techniques or equipment that’s super precise.
Size and Placement: Figure out how big your design is and where it’s going to go on the molded parts. Think about the printing area’s dimensions and make sure your screen printing gear can handle the size you need.
Color Considerations: Check out how many colors you’ve got in your design. If it’s got lots of colors, you might need equipment with multiple stations or heads to make sure the colors line up perfectly.
Artwork Compatibility: Make sure your artwork or design files are in a format that works well for screen printing.
Ink Selection: Pick the right kind of ink based on what material your injection molded parts are made of. There are different inks for printing on plastics, metals, and other stuff. Just make sure the ink and the material get along.
Durability and Resistance: Think about how tough your printed design needs to be, especially if the injection molded parts will be dealing with rough environments or getting a lot of wear and tear. Choose inks and printing methods that can handle whatever the parts will face.
Screen Printing Product Acceptance Standards
As a plastic product designer, you sent your design to the injection molding factories for products. You would certainly want to know the quality inspection reference standards for screen printing processing of plastic products, to have a foundational basis for daily communications with manufacturers. Since standards vary across different enterprises, we can only provide some thoughts for your reference:
I. Environment for Inspecting Screen Printed Items
- Illuminance: 200-300LX (equivalent to a 40W fluorescent lamp at a distance of 750MM)
- The product to be inspected should be approximately at a 45° angle to the inspector’s line of sight (as shown in the diagram), for about 10 seconds.
- Distance between the inspector’s line of sight and the surface of the product to be inspected:
- Class A surface (directly visible external surface): 400MM
- Class B surface (less obvious external): 500MM
- Class C surface (internal and external surfaces that are hard to observe): 800MM
II. Common Defects in Screen Printed Items
- Foreign objects: Dust, dot-like, or filamentous foreign objects adhered to the coating after screen printing.
- Exposure: Underprinting due to too thin application.
- Missing print: Required screen printing area not printed.
- Blurry/Discontinuous lines: Poor screen printing resulting in uneven thickness, blurry images, and partially disconnected lines.
- Uneven screen printing thickness: Due to improper screen printing operation, resulting in uneven thickness of dots, lines, or patterns.
- Misalignment: Due to inaccurate screen printing position, resulting in shifted print.
- Poor adhesion: Insufficient adhesion of the screen printing coating, which can be peeled off with 3M tape.
- Pinholes: Pinhole-like small holes visible on the surface of the coating.
- Scratches/Scuffs: Caused by inadequate protection after screen printing.
- Foreign colors/Stains: Non-screen printing colors adhered to the screen printing surface.
- Color difference: Color deviation compared to the standard color board.
III. Screen Printing Reliability Test Methods
FirstMold provides the following 15 test methods, which each injection molded product user can select according to their enterprise’s needs.
1. High-Temperature Storage Test
- Storage temperature: +66°C
- Duration: 48 hours
- Acceptance criteria: After removal from storage, the printed surface should show no wrinkles, bubbling, cracks, or peeling, and no significant change in color or glossiness after 2 hours at room temperature.
2. Low-Temperature Test
- Storage temperature: -40°C
- Duration: 48 hours
- Acceptance criteria: Similar to the high-temperature storage test.
3. High Temperature and High Humidity Storage Test
- Temperature/Humidity: +66°C/85%
- Duration: 96 hours
- Acceptance criteria: Similar to the high-temperature storage test.
4. Thermal Shock Test
- Storage temperature: -40°C/+66°C
- Cycle description: One cycle consists of a temperature change from -40°C to +66°C within a maximum of 5 minutes, for a total of 12 cycles.
- Acceptance criteria: After the test, the parts and printed surfaces should show no wrinkles, bubbling, cracks, peeling, and no significant change in color or glossiness after 2 hours at room temperature.
5. Screen/Pad Printing Adhesion Test
- Purpose: To assess the adhesion of screen/pad printing inks.
- Tools: 3M600 clear tape or transparent tape with adhesion strength greater than 5.3N/18mm.
- Method: Apply the 3M600 clear tape to the printed fonts or patterns on the test sample, press down by hand to ensure adherence, then peel off the tape at a 90-degree angle to the test surface, repeating at the same area three times.
- Acceptance criteria: Visual inspection of the surface should reveal clear and distinguishable fonts or patterns with no peeling.
6. Friction Test
- Purpose: To evaluate the adhesion of paint on the surface as well as screen/pad printed inks.
- Equipment: Eraser.
- Method: Secure the sample and apply a vertical force of 500G over a 15MM stroke back and forth, counting each round trip as one cycle, for a total of 50 continuous cycles on the screen/pad printed fonts or patterns.
- Acceptance criteria: Visual inspection of the surface should show no wear to the base material, with clear and distinguishable screen/pad printed patterns or fonts.
7. Solvent Resistance Test
- Isopropyl Alcohol Test: Apply 1ml of isopropyl alcohol solution on the spray-coated or screen printed surface of the sample. After 10 minutes, wipe off the alcohol solution with a white cloth.
- Alcohol Resistance Test: Wet a cotton ball or white cloth with 99% alcohol solution, then rub back and forth at the same spot on the sample’s printed fonts and patterns with 1kg pressure and a speed of one back-and-forth motion per second for 20 times.
- Acceptance criteria: After wiping, the printed fonts or patterns on the sample surface should be clearly visible, with no loss of glossiness or color change.
8. Thumb Test
- Conditions: More than 5 samples.
- Procedure: Rub the printed image with a thumb applying a force of 3+0.5/-0KGF back and forth 15 times.
- Acceptance Criteria: The printed pattern should not show any gaps/breaks/ink adhesion issues, otherwise, it is considered as not acceptable.
9. 75% Alcohol Test
- Conditions: More than 5 samples, white cotton cloth, 75% alcohol, and a weight of 1.5+0.5/-0KGF.
- Procedure: Attach the white cotton cloth to the bottom of the 1.5KGF weight, soak it in 75% alcohol, and then rub back and forth over the printed pattern for 30 cycles (about 15 seconds).
- Acceptance Criteria: The printed pattern should not show peeling, gaps, breaks, or poor ink adhesion. Slight fading of color is permissible, but the printed pattern must remain clear and not blurred. Otherwise, it is considered not acceptable.
10. 95% Alcohol Test
- Conditions: More than 5 samples, white cotton cloth, 95% alcohol, and a weight of 1.5+0.5/-0KGF.
- Procedure: Similar to the 75% alcohol test, using 95% alcohol.
- Acceptance Criteria: Identical to the 75% alcohol test, ensuring the printed pattern’s integrity and visibility despite slight allowable color fading.
11. 810 Tape Test
- Conditions: More than 5 samples, 810 tape.
- Procedure: Fully adhere the 810 tape to the screen-printed surface, then pull the tape off quickly at a 45-degree angle. Repeat this process three times.
- Acceptance Criteria: The printed pattern should not show gaps or breaks after the tape test.
12. 3M600 Tape Test
- Conditions: More than 5 samples, 3M600 tape.
- Procedure: Apply the 3M600 tape fully onto the screen-printed surface and pull it off quickly at a 45-degree angle. This test is done once.
- Acceptance Criteria: Similar to the 810 tape test, the printed pattern should remain intact without showing gaps or breaks.
13. 250 Tape Test
- Conditions: More than 5 samples, 250 tape.
- Procedure: Similar to the 810 tape test, using 250 tape and repeating the process three times.
- Acceptance Criteria: The printed pattern must not display gaps or breaks, ensuring the adhesion and durability of the screen printing.
14. Gasoline Wiping Test
- Conditions: More than 5 samples, white cotton cloth, gasoline:75% alcohol mixture (1:1 ratio), and a weight of 1.5+0.5/-0KGF.
- Procedure: Attach the white cotton cloth to the bottom of the 1.5KGF weight, soak it in the gasoline:alcohol mixture, and rub back and forth over the printed pattern for 30 cycles (about 15 seconds).
- Acceptance Criteria: The printed pattern should not show peeling, gaps, breaks, or poor ink adhesion. Color fading is allowable to some extent, but the pattern must remain clear and not blurred.
15. Hexane Rub Test
- Conditions: More than 5 samples, white cotton cloth, hexane, and a weight of 1.5+0.5/-0KGF.
- Procedure: Attach the white cotton cloth to the bottom of the 1.5KGF weight, soak it in hexane, and rub back and forth over the printed pattern for 30 cycles (about 15 seconds).
- Acceptance Criteria: Similar to the gasoline wiping test, with emphasis on the printed pattern’s clarity and adhesion despite allowable slight color fading.
In Conclusion
The content of this article about screen printing is quite extensive, covering the concept, applications, acceptance standards, design considerations, and more. As a demander of injection molded products or a product designer, you may need to be familiar with these topics to some extent.
I am Lee Young, a production expert at FirstMold. If you have any questions about screen printing or other surface treatment methods for injection molded products, please feel free to email us at [email protected] for further discussion.